The University of Houston is collaborating with Texas A&M University to tackle the challenge hindering the use of Additive Manufacturing (AM), commonly known as 3D printing, for a variety of commercial applications – the need for real-time monitoring and analysis to ensure consistent quality and reproducibility throughout the production process.
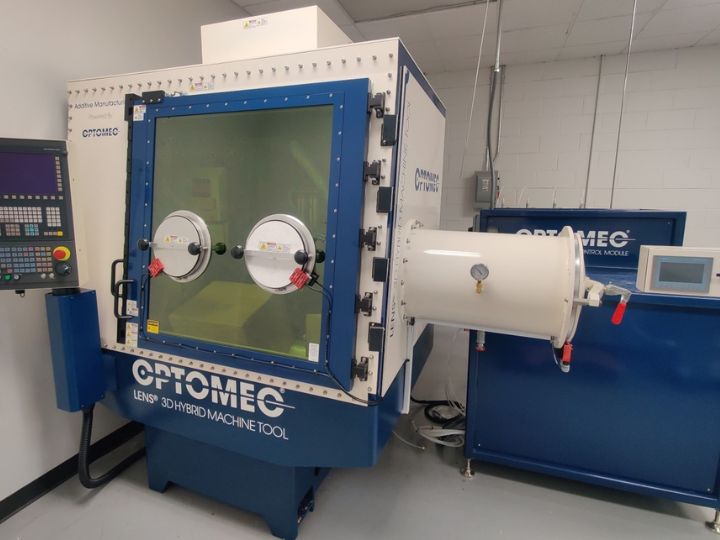
At present, quality control and qualification of metal AM parts is mostly carried out through offline inspection and characterization, but ideally, a broad range of sub-surface and bulk microstructural features should be evaluated in real-time, at the speed of fabrication in an AM tool.
“The objective of our project is to accomplish this goal by the development of real-time, comprehensive, in-situ sub-surface and bulk structural analysis of AM parts during fabrication, and integration with multi-modal data from various in-situ sensors, that can bridge the critical knowledge gap between process conditions and properties,” said Venkat Selvamanickam, M.D. Anderson Professor of Mechanical Engineering at UH, who is leading the project through the UH Advanced Manufacturing Institute (AMI), which he created. The project is supported by a $957,849 grant from NIST The National Institute of Standards and Technology.
Preliminary study has confirmed that sample-to-sample differences due to varying AM process conditions are identifiable via two-dimensional X-ray diffraction (2D-XRD).
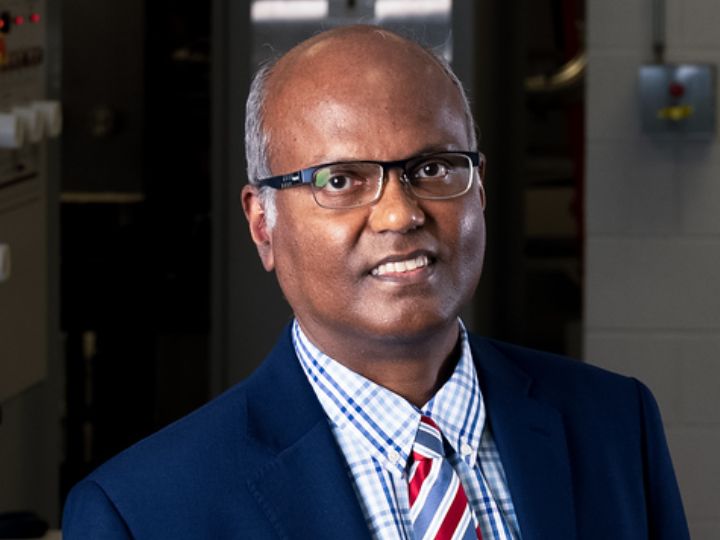
“We will design, construct and install a custom in-line 2D-XRD in the hybrid Directed Energy Deposition tool in AMI facilities at University of Houston. This tool offers a robust platform that includes features such as multi-material deposition (for spot-alloying and functional grading) and several in-situ sensors for process monitoring,” said Selvamanickam.
Since its formation in 2018, AMI, a University-wide center, serves as a pivotal hub for advancing the scale-up and commercialization of technologies developed by UH faculty, facilitating the transition from idea to manufacturing and eventual market deployment. The project on additive manufacturing follows a successful track record of AMI in scaling up superconductor manufacturing technologies for industrial applications.
Ying Lin, associate professor of industrial engineering and Goran Majkic, research professor of mechanical engineering at UH join Selvamanickam on the research team. At Texas A&M University, Ali Erdemir, professor of mechanical engineering and Halliburton Chair, will coordinate the program and the Texas A&M team includes Mathew Kuttolamadom, associate professor of engineering technology and industrial distribution.
To be sure, AM is revolutionizing the way metal structures are fabricated for many applications in aerospace, automotive, energy, medical and other industries. But widespread use of is contingent on meeting the stringent requirements of quality and repeatability of parts made by this process.
“Such an achievement will tremendously expand the use of metal additive manufacturing in many applications,” said Selvamanickam.