Developing Bio-Inspired Buoyancy Control for Subsea Service AUVs
Status: AWARD END DATE: 08/31/22
Background:
Humans have created robots to help us perform tasks underwater. It will not be too long before we will see robots fully automate deepwater Gulf of Mexico exploration, production, and decommissioning. Subsea industry is quickly moving toward deeper waters, complex, challenging, and dynamic working environments, while requiring the highest level of safety. Tasks that have been historically undertaken by workers in shallow waters are now performed by Remotely Operated underwater Vehicles (ROV) at water depths that humans cannot support. Work-class ROVs (WROV), in particular, are being used for surveillance as well as for intervention.
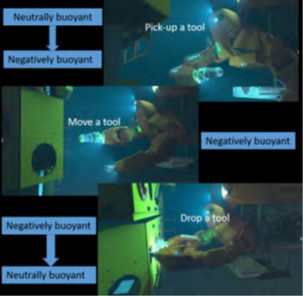
ROVs suffer from several limitations including requirement of a large operating crew, a need of a dynamically positioned surface vessel, tether management, and high cost mobilization and demobilization. Autonomous Underwater Vehicles (AUV) are now emerging with new capabilities and technologies that could make them more efficient and more cost effective than ROVs. Hydrocarbon development environments of deep and ultra-deep water in the Gulf of Mexico and other regions in the world require AUVs that can autonomously operate in confined spaces and can perform forceful interactions with the assets. Hence, new paradigms in shape, autonomy, sensing and communication and physical capabilities are needed to make AUVs the tool of choice for deepwater industry.
Currently, subsea robots are built rigid and neutrally buoyant so that their volume remains unchanged despite the changing fluidic pressure. Although they are normally big and heavy, underwater service robots can take advantages of their neural buoyant state to save energy when they are maneuvering and operating in subsea environments. However, when ROVs perform tasks such as picking and placing tools or collecting disassembled parts in offshore asset's monitoring, repairing, and decommissioning, they will deviate from the neutral buoyancy state. Under such circumstances, the service robots must constantly actuate to maintain their depth, which is energy inefficient as was recently demonstrated by the PIs. AUVs rely on their thrusters and possibly a ballast to actively control buoyancy. This is achieved by thruster and pump control. If AUVs are involved in forceful interactions including lifting objects or executing a forceful act, thrusters and a ballast may not be fully adequate for real-time buoyancy control.
Additional Media Assets:
Industry Impact:
Constantly monitoring and repairing subsea infrastructures and equipment play important roles in extending the lifetime of those multi-million-dollar offshore assets. Decommissioning of offshore assets also call for underwater service robots to disassemble the subsea infrastructures and cleanup the sea floor environment.
Fine distributed buoyancy control, which is not feasible with current thruster/ballast mechanisms, will enable adaptive maneuvering and forceful interaction with the environment in confined spaces similar to how marine swimmers do. A combination of the traditional thruster/ballast mechanism for gross buoyancy and motion, and the proposed soft robotics mechanism (fuel cells/water electrolysers) for fine and distributed buoyancy will undoubtedly provide AUV's with unprecedented capabilities. The broader impact of this research includes the opportunities created in exploring and expanding solid state fuel cell/electrolyzing technology as a soft robotics mechanism to address immediate exploration and production challenges in the Gulf of Mexico. The results of this research will be valuable not only to international deepwater oil and gas markets, but also to subsea renewable energies and subsea mining.
Project Goals:
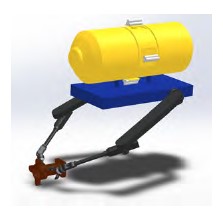
Carrying and Processing a Load
Tasks:
- Develop Buoyancy Control Device Enabled by Reversible Fuel Cells
- Task 1.1: Design a self-enclosed buoyancy control device to house an IPMC electrolyzer, a micro fuel cell, and two gas chambers. Demonstrate an open-loop control test
- Task 1.2: Develop a back-stepping nonlinear control with a nonlinear observer
- Task 1.3: Demonstrate an close-loop control of the BCD which can oat and sink with a large depth change (more than 3 m)
- Develop an Underwater Service Robot
- Task 2.1: Develop two water-proof robotic grippers
- Task 2.2: Integrate two BCDs and robotic grippers into the AUV
- Task 2.3: Open-loop control test of underwater service robot
- Modeling and Control
- Task 3.1: Develop 3D nonlinear dynamic model of the service robot
- Task 3.2: Develop depth control for the service robot
- Task 3.3: Develop orientation control of the service robot
- Comprehensive Test at NASA's Neutral Buoyancy Lab (NBL)
- Senior Design Competition Between UH and Rice
Gantt Chart:
Highlights:
- Developed a gas consumption rate control
- Fabricated a service robot integrating a blue ROV, four BCDs, and a robotic gripper
- Developed a nonlinear dynamic model of the service robot
- Developed depth and orientation control using both hard and soft actuators for the service robot
- Validated the control in simulation
Keyfindings:
- Developed a volume-to-electricity engine enabled by reversible fuel cell
- Developed buoyancy control device (BCD) using that engine
- Developed a service robot with BCDs and robotic gripper
- Developed a 6-DOF dynamic model for the service robot
- Developed a hybrid control of hard and soft actuators for both depth and orientation control.