2021 TIEEP Water Forum Thursday, May 6, 2021, 4:20-5:50 pm
Theme: Reducing Water Use in Manufacturing Plants
Despite the hurricanes and high rainfall along the Gulf Coast, we do experience times of drought and water shortages in Texas; and globally, access to clean water is a major sustainability concern. Water is also inextricably linked to energy: We need energy to pump and to manage water, and we use large amounts of water in our energy systems – for example, steam and cooling water. In this water forum, we explore tools and technologies for reducing water use in manufacturing plants. This includes presentations from two vendors on innovative processes and equipment, and one presentation on a DOE software package to aid understanding, managing, and improving water balances. Not only can these resources save water; they can also lead to energy savings, space savings, quality improvements, and reductions in capital and operating costs for new plants and revamps.
The Water Forum will be followed by the STS-AIChE Monthly Virtual Dinner Meeting at 6:00 pm, where Ann Rosenberg, SVP for Sustainable Development at Wood plc., will speak on Energy 2.0 and the Race to Net Zero and Resilience. Water Forum participants are invited to stay for her presentation. PDH certificates will be available for both the Water Forum and the STS-AIChE meeting.
RECORDED SEGMENTS
WATER FORUM SEGMENTS
Reduced Life-Cycle Costs and Enhanced Sustainability of Wastewater Treatment Utilizing AquaNereda® Aerobic Granular Sludge Technology
Segment Overview:
The AquaNereda® technology provides advanced biological wastewater treatment using the unique features of aerobic granular biomass composed of granular sludge. The technology has been used successfully for more than 15 years in full-scale wastewater treatment facilities, with over 80 plants currently in operation or under design and construction.
There are many distinct advantages AquaNereda® offers compared to conventional biological treatment, including up to 50-percent energy savings by eliminating the need for sludge recirculation pumps, mechanical mixing and optimized aeration utilization; up to a 75-percent smaller footprint due to elimination of primary and secondary clarifiers, sludge pumping systems, and separate aerobic, anoxic and anaerobic selector basins; excellent effluent quality without chemical addition; robustness and resilience to toxic shocks and influent load fluctuations; and easy operation with automated adjustable cycle structure.
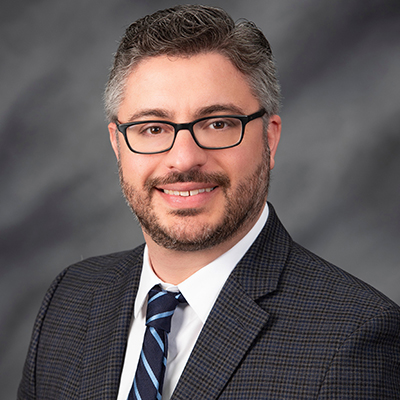
jtardio@aqua-aerobic.com | 815-639-4451
Joe holds a Bachelor’s Degree in Biological Sciences and Chemistry from the University of Delaware and a Master’s Degree in Environmental & Waste Management from Stony Brook University. He also holds a Credential of Readiness from Harvard Business School Online. Joe has management experience with a broad range of innovative water and wastewater treatment technologies, including biological, filtration and separation products. He is an experienced technical presenter to both clients and engineers.
Joe has domestic and international experience in the water and wastewater treatment industry since 2006. Prior to his current role, Joe’s previous positions include Senior Sales Engineer, Market Sales Manager, Regional Manager and Vice President of Sales. He is a published author of several technical papers in AWWA/AMTA and WEF proceedings and a past instructor for AWWA operator training. He has conducted molecular biology research which has contributed to the sustainable management of nitrogen within the agricultural industry.
DOE’s Plant Water Profiler Tool for Water Assessment of Manufacturing Facilities
Segment Overview:
The DOE’s Plant Water Profiler Tool (PWP), developed at Oak Ridge National Laboratory (ORNL), is a comprehensive tool designed to help conduct a facility level water assessment of a manufacturing plant. The tool, based on water mass balance analysis, helps identify and account for water procurement and use in manufacturing operations, recognize the true cost of water, and identify potential areas for water and associated cost savings. Results can also be used to establish a baseline and track water use during subsequent years. Further, PWP assesses the water efficiency status of a plant and its individual systems and provides a tailored list of water efficiency measures and opportunities specific to the plant.
Thus, PWP is a first step that industrial manufacturing plants can take to identify opportunities for minimizing water use and reducing cost. Additionally, governments or private organizations can use this tool as a survey to help build a database of industrial water use.
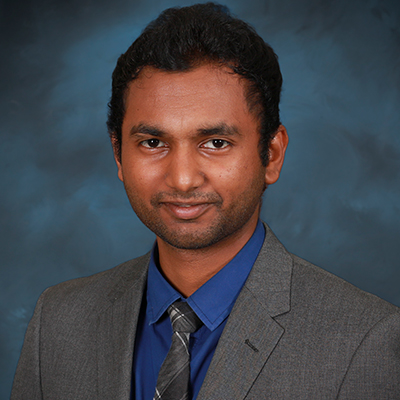
thirumarank@ornl.gov | 865-574-8754
Kiran Thirumaran is an R&D staff member at Oak Ridge National Laboratory (ORNL) and has been working on industrial efficiency since 2012. Kiran is a Technical Account Manager for the Department of Energy’s Better Buildings, Better Plants Program where he works closely with over 15 major companies to assist them in implementing energy and water management strategies and optimizing facilities.
Through the Better Plants program, Kiran has supported the development of numerous tools and resources for industries including the Plant-Water Profiler (PWP) tool and associated in-plant training.
Kiran also leads ORNL’s support activities for the National Alliance for Water Innovation (NAWI) which seeks to address water security issues in the United States. Kiran holds a Master’s degree in Mechanical Engineering from North Carolina State University where he was heavily involved with his university’s Industrial Assessment Center.
Introduction to Voltea’s Membrane Capacitive Deionization (CapDI) Water Treatment Technology, and its Applications
Segment Overview:
Voltea’s Membrane Capacitive Deionization (CapDI) Technology is a low energy, high recovery option for Total Dissolved Solids (TDS) reduction and water treatment. I would like to introduce you to this innovative water treatment technology, explaining how it works, as well as sharing its advantages over other traditional treatment methods. Armed with this information a number of case studies will be shared establishing the breadth of this technology in existing installations ranging from cooling tower make up water through to wastewater treatment and recycling applications. These examples will demonstrate how CapDI can reduce water usage, minimize costs, improving operation and performance with your industry and companies.
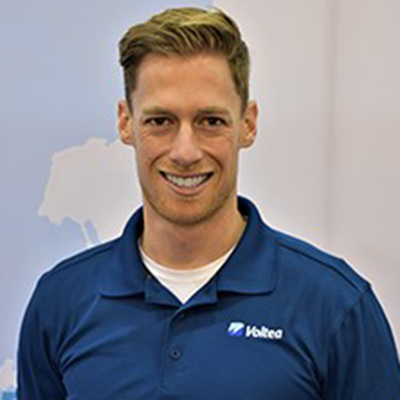
Joshua.summers@voltea.com | 404-414-4291
Josh Summers was born and educated in the UK, holding a Master’s degree in Chemistry. He has worked for Voltea since 2011, progressing through the company; initially joining the R and D team, leading the Service team, and now manages Sales in North America.
This progression allows a good breadth of knowledge of CapDI technology and the water industry ensuring the customer always receives the best service and results.